How to Benchmark Manufacturing Costs Globally
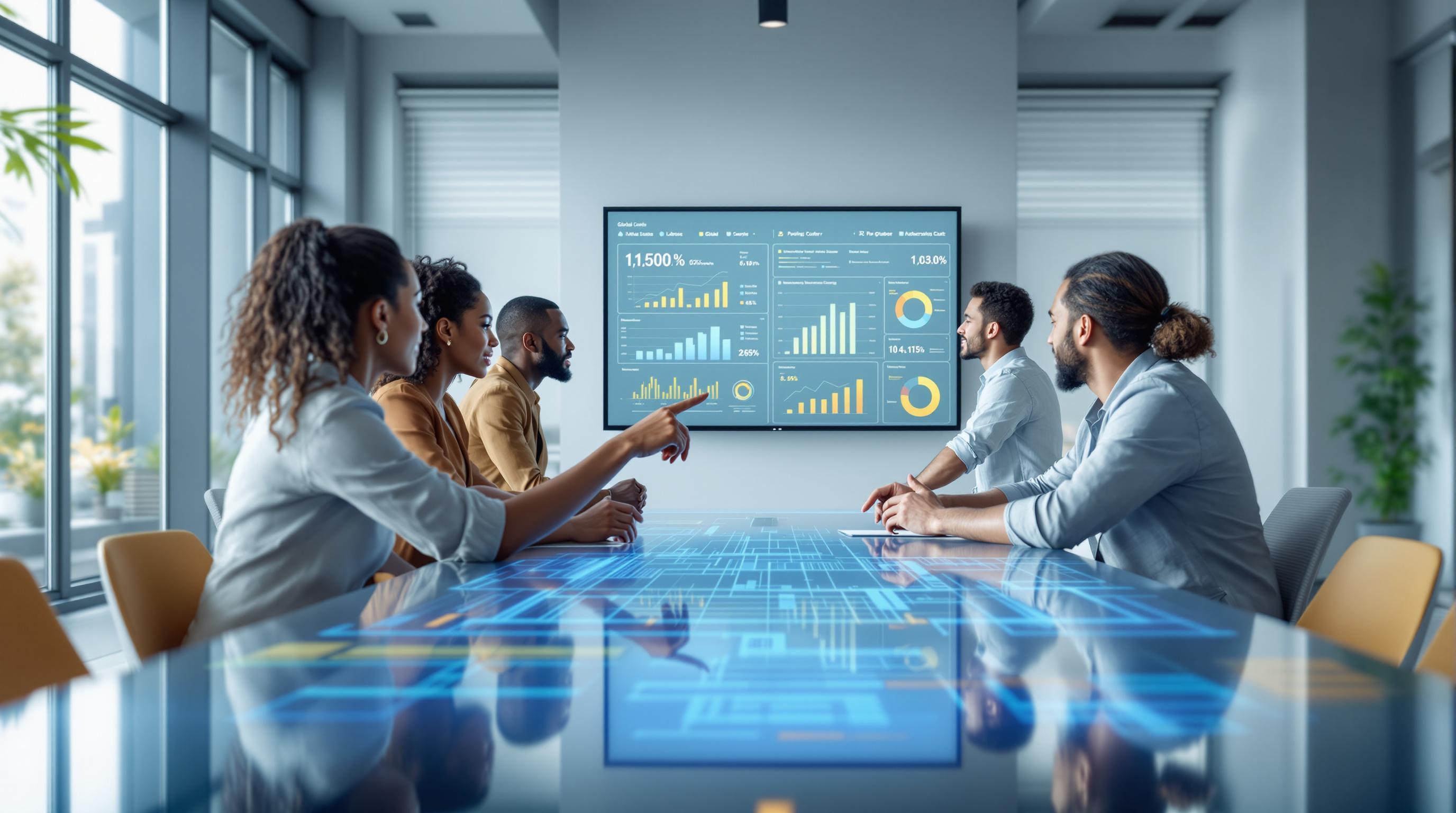
Want to cut manufacturing costs and improve efficiency? Benchmarking global manufacturing expenses is your answer. Here’s a quick guide to help you identify cost-saving opportunities, compare regions, and make informed decisions about production.
Key Highlights:
- Main Cost Drivers: Labor, materials, and shipping costs vary by location.
- Data Sources: Use market reports, supplier invoices, and cost analysis services for accurate comparisons.
- Key Metrics: Labor cost per unit, full delivery cost, and location cost rankings.
- Regional Adjustments: Factor in exchange rates, productivity, and long-term costs like maintenance and infrastructure.
- Actionable Steps: Regularly monitor costs, identify inefficiencies, and evaluate facility locations.
By following these steps, you can optimize manufacturing decisions and stay competitive in a changing global market. Let’s dive deeper into each aspect.
Step 1: Main Manufacturing Cost Elements
When comparing production costs across the globe, it's crucial to break down the key factors that influence expenses: labor, materials, and shipping. These vary by location and directly affect overall costs.
Workforce Expenses
Labor costs play a big role in manufacturing. Key considerations include:
- Base wages and overtime rates
- Contributions to social security and healthcare
- Investments in employee training and skill development
- Adherence to local labor laws and regulations
It's important to evaluate not just wages but also productivity levels in each region to get a complete picture of workforce expenses.
Materials and Supply Costs
Raw materials are often one of the largest expenses in manufacturing. Factors influencing these costs include:
- Availability of materials locally and how long it takes to procure them
- Import duties and taxes
- Discounts for bulk purchasing
- Regional differences in quality standards
Understanding the local market and supply chain conditions can help you better estimate material costs in different regions.
Shipping and Transport Fees
Shipping costs go beyond just carrier charges. Be sure to factor in:
- The distance between manufacturing facilities and shipping ports
- Additional fees like fuel surcharges or container costs
- Customs clearance processes and associated delays
- The quality of regional infrastructure, which can impact delivery times and risks
Don't overlook indirect costs like potential delays, damages, or inventory storage fees - they can add up quickly and affect the total cost of getting products to their destination.
Step 2: Finding Cost Data Sources
Once you've broken down the cost drivers, the next move is to pinpoint reliable sources for cost data. Accessing diverse, trustworthy sources is key to understanding global manufacturing costs and ensuring accurate comparisons.
Market Reports and Databases
Databases are a great starting point for gathering baseline cost data across different regions. For example, the World Bank Enterprise Surveys offer wage insights by region, while the UN Comtrade Database provides details on material imports and exports.
Direct Cost Information
For precise production figures, dive into direct cost information. Supplier invoices are particularly useful for identifying exact production costs and spotting pricing trends over time.
Cost Analysis Services
Specialized services like Phoenix Strategy Group can take your cost analysis further. They compare manufacturing expenses across regions, highlight potential savings, and assess the long-term impact of location choices.
Step 3: Key Cost Comparison Measures
Once you've identified cost components and gathered data, the next step is to use specific metrics to compare costs across different locations. This involves looking at both obvious costs and hidden expenses to get a clear picture.
Labor Cost Per Unit
Labor cost per unit isn't just about hourly wages. While lower wages might seem attractive, they can be offset by factors like lower productivity, higher automation expenses, or additional costs such as training and employee turnover.
To calculate labor cost per unit:
- Track total labor hours (both direct and indirect)
- Measure the number of units produced
- Adjust for differences in regional productivity
- Include extra costs like training and turnover
A helpful metric here is units produced per labor hour (UPLH). This can show that higher-wage locations might actually have lower per-unit costs due to better efficiency or automation. By combining this with your earlier labor cost breakdown, you'll get a more complete understanding of labor-related expenses.
Once you've analyzed labor costs, move on to the broader picture with a full delivery cost assessment.
Full Delivery Cost
Manufacturing costs don't stop at production. A full delivery cost analysis should include:
- Raw material costs, adjusted for local pricing
- Energy costs, which can vary greatly by region
- Duties and tariffs for imports and exports
- Transportation costs, including inland and ocean freight
- Inventory carrying costs, which can significantly impact product value
- Quality control and rework expenses
By gathering accurate, location-specific data, you'll create a detailed model of the total costs involved in delivering your product.
Location Cost Rankings
To compare manufacturing costs across regions, standardized rankings are often used. These rankings typically factor in:
- Stability of the labor market
- Quality of infrastructure
- Reliability of energy supply
- Political and regulatory risks
- Currency fluctuations
Many analysts and research firms publish manufacturing cost indices, often using a major market like the United States as a baseline. These indices change over time with shifts in wages, regulations, and economic conditions, so keeping your data up to date is crucial.
sbb-itb-e766981
Step 4: Regional Cost Comparison Methods
Once you've identified cost components and data sources, the next step is adjusting for regional differences. These adjustments are crucial for accurate international cost comparisons.
Exchange Rate Adjustments
To align costs across regions, use these strategies:
- Use a rolling 12-month average exchange rate to minimize short-term fluctuations.
- Apply purchasing power parity (PPP) rates for better precision in comparisons.
- Factor in forward exchange rates when planning for long-term investments.
Keep calculations in USD for consistency in global comparisons, while also accounting for regional inflation. This ensures a solid foundation for evaluating production outcomes.
Output and Quality Differences
Assess the effectiveness of production by focusing on these key metrics:
- Productivity: Measure units per hour, defect rates, machine usage, and worker efficiency.
- Quality: Review compliance with control processes, certification standards, rework rates, and material waste.
- Technology: Consider automation levels, equipment sophistication, process control, and the technical expertise of the workforce.
These evaluations help paint a clear picture of long-term cost implications.
Long-term Cost Impact
When analyzing long-term expenses, consider these factors:
Maintenance and Support
- Availability of local expertise for equipment maintenance.
- Impact of regional support infrastructure on daily operations.
- Training needs specific to the region.
Warranty and Quality Costs
- Differences in defect rates across regions.
- Customer support and service costs.
- Transportation expenses for repairs or replacements.
Infrastructure Investment
- Reliability of power supply in the region.
- Requirements for water treatment systems.
- Variations in climate control needs.
Additionally, be aware of potential cost increases from:
- Rising wages in developing regions.
- Compliance with environmental regulations.
- Investments in infrastructure and technology upgrades.
To fully understand regional cost differences, project these expenses over a 5-year period. This long-term view complements earlier analyses, helping to identify areas for sustained cost efficiency.
Step 5: Using Cost Data for Decisions
Once you've established cost components and comparative metrics, it's time to use that data to guide your decisions.
Identifying Cost-Saving Opportunities
Dive into your cost data to uncover areas where expenses can be reduced:
Labor Efficiency
- Review shift schedules and overtime policies for potential adjustments.
- Assess training programs to boost worker productivity.
- Look into automation for repetitive tasks to save time and money.
Managing Material Costs
- Consolidate vendors to streamline sourcing.
- Negotiate bulk pricing agreements with suppliers.
- Set measurable waste reduction goals with clear KPIs.
Improving Processes
- Simplify production workflows to cut unnecessary steps.
- Reduce machine setup times to increase operational efficiency.
- Lower inventory holding costs by optimizing stock levels.
Evaluating Plant Locations
When deciding on manufacturing locations, consider these critical factors:
Infrastructure
- Assess power reliability and associated costs.
- Examine the quality of local transportation networks.
- Evaluate the strength of the local supplier ecosystem.
Risk Factors
- Consider political and economic stability in the region.
- Evaluate exposure to natural disasters.
- Ensure adequate protection for intellectual property.
Workforce
- Check the availability of skilled labor in the area.
- Understand local labor law requirements.
- Assess the availability of training resources for employees.
Using a weighted scoring system can help you balance cost savings with operational risks and strategic benefits. Incorporate these findings into your regular cost review process to maintain a competitive edge.
Conducting Regular Cost Reviews
Monthly Monitoring
- Track direct labor costs per unit.
- Monitor changes in material prices.
- Review energy consumption trends.
- Keep an eye on quality-related expenses.
Quarterly Evaluations
- Analyze productivity patterns.
- Investigate reasons behind cost variances.
- Measure the impact of improvement initiatives.
- Assess how market conditions are influencing costs.
Annual Strategic Assessment
- Examine long-term cost trends.
- Identify technology investments that could lower costs.
- Evaluate the effectiveness of your location strategy.
- Review the value of supplier relationships.
Implement a standardized reporting system to quickly identify trends and anomalies in your costs. Set up automated alerts for any significant deviations, so you can address potential problems early and take corrective action when needed.
Conclusion: Building Cost-Effective Manufacturing
Key Takeaways
To effectively benchmark manufacturing costs, focus on the main cost drivers and make decisions based on hard data. Breaking down and tracking core cost components can uncover clear opportunities to cut costs.
Here’s what matters most for successful global cost benchmarking:
- Reliable data: Use accurate market intelligence and verified cost information.
- Standardized metrics: Apply consistent measurements across all locations.
- Ongoing tracking: Regularly monitor costs and analyze trends.
- Risk management: Weigh cost savings against operational stability.
- Strategic alignment: Ensure cost decisions align with long-term business goals.
Use these principles as a foundation for a focused and effective benchmarking approach.
How to Begin
Start your benchmarking efforts by targeting areas with the most potential for cost savings. A good way to begin is by running a pilot analysis at a single facility. This initial step allows you to:
- Set baseline cost metrics.
- Test your data collection and reporting methods.
- Confirm assumptions about potential savings.
For more complex benchmarking efforts, consider working with experts like Phoenix Strategy Group (https://phoenixstrategy.group). Their services provide:
- Access to extensive cost databases.
- Insights into global manufacturing trends.
- Advanced analytics tools.
- Risk assessment strategies.
- Support for implementation.
The key to success is staying consistent in your analysis while staying flexible enough to adjust to market shifts. Regularly updating your data ensures it remains useful for making informed, strategic decisions.